Robots, robots, robots. Eso es probablemente lo que uno evoca si trata de imaginar la fábrica del futuro. Pero los robots –o la automatización– son solo una de las formas en que está cambiando la fabricación.
Las fábricas también se están volviendo modulares y escalables, más fáciles de mantener, acceder y de solucionar problemas, así como interoperables –diseñadas de tal manera que las diversas interfaces tecnológicas puedan trabajar en conjunto sin problemas–. Además, deben ser sostenibles, no solo para cumplir con las exigencias cada vez más estrictas de gobiernos y consumidores, sino también para garantizar la eficiencia.
Esto es similar a las tendencias observadas en las ciudades inteligentes, por lo que las fábricas podrían considerarse “canarios en la mina” en lo que respecta al futuro de la vida urbana. A su vez, las fábricas inteligentes se centran en reducir los desperdicios y el consumo de energía, en línea con los objetivos de sostenibilidad de las ciudades inteligentes. Las fábricas eficientes contribuyen a reducir las emisiones y el uso de recursos en las zonas urbanas.
Las empresas están adoptando cada vez más esta visión. Por ejemplo, Schaeffler, una compañía alemana que produce piezas de automóviles, presentó sus planes para establecer “fábricas inteligentes”. Estas incluyen el uso de herramientas digitales para crear modelos 3D de las futuras instalaciones, operaciones totalmente conectadas en red para permitir el intercambio constante de datos y un diseño adaptable que pueda modificarse fácilmente para fabricar nuevas piezas.
Esto representa una enorme oportunidad de crecimiento para las empresas capaces de ayudar a crear estas fábricas. Se prevé que el mercado global de software industrial alcanzará los USD 355.000 millones en 2030, lo que supone una tasa de crecimiento anual compuesto (TCAC) de aproximadamente el 13,5% (véase el gráfico). También se espera que crezca el sector de la tecnología operativa, o hardware.
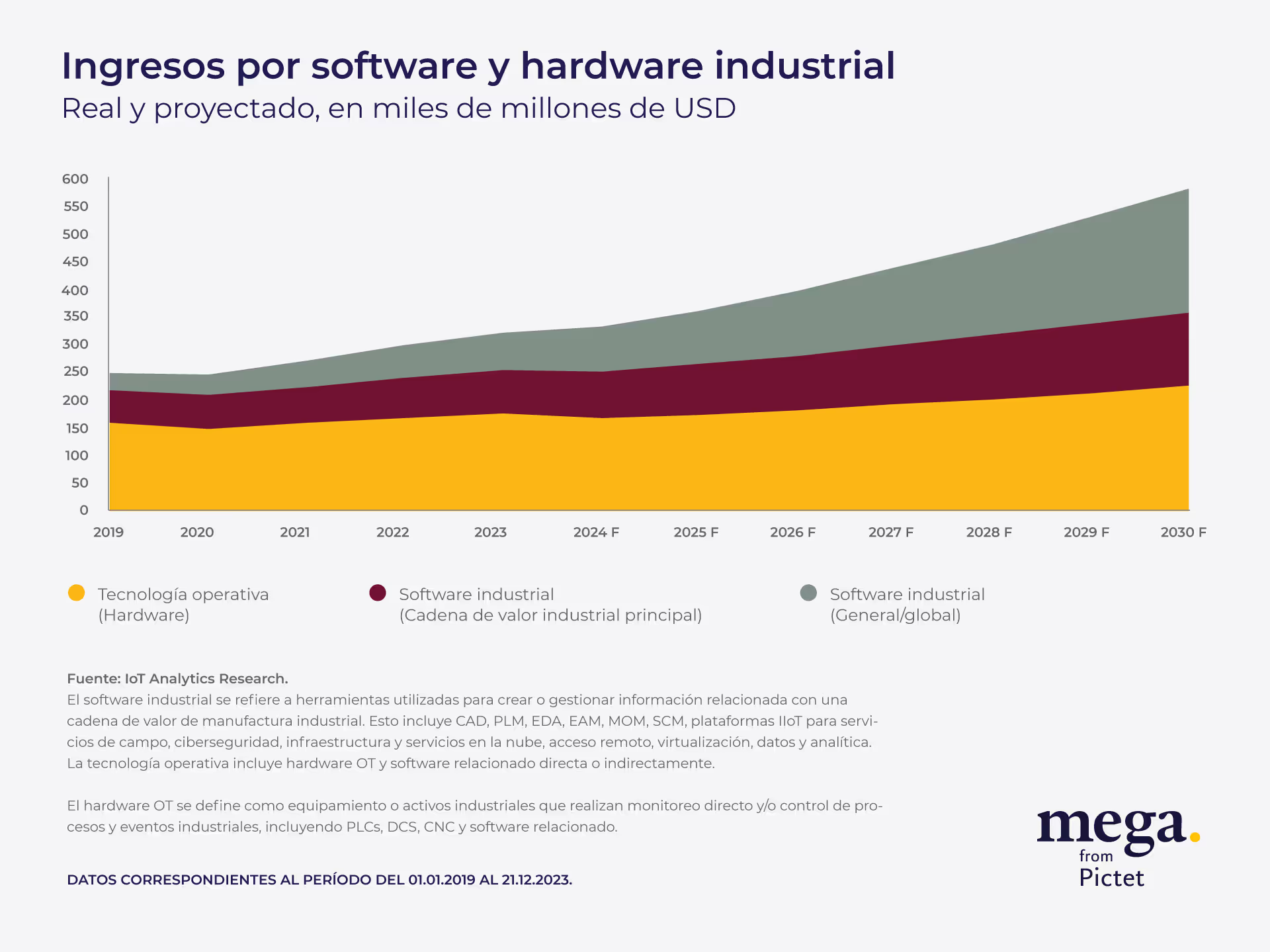
Los cambios globales en la producción –como el re-shoring a Estados Unidos, el near-shoring o el traslado desde China a Vietnam o India– están dando lugar a la creación de nuevas fábricas, lo que a su vez supone una oportunidad para que las empresas adopten las últimas tecnologías.
Además de la creación de nuevas plantas, también observamos una creciente demanda de modernización de instalaciones existentes: desde la automatización de líneas manuales hasta la actualización de las ya automatizadas. Asimismo, las nuevas normativas sobre sostenibilidad están impulsando a las empresas a instalar sensores inteligentes y nuevas plataformas de software para monitorear y gestionar mejor sus indicadores de sostenibilidad.
El proceso en las fábricas inteligentes comienza con sensores que recogen información en tiempo real sobre temperatura, presión, velocidad y otros parámetros. Los datos se envían a los sistemas de control (conocidos como controladores lógicos programables –PLC– y sistemas controlados distribuidos –DCS–), que los utilizan para comunicarse con los actuadores, dispositivos que pueden ajustar el comportamiento de las máquinas, por ejemplo, encendiendo un motor o abriendo una válvula. Este proceso enlaza el mundo digital con la fabricación física. Por encima de todo ello están los sistemas de supervisión de nivel superior, los programas informáticos y los sistemas de planificación empresarial.
En el software industrial, notamos un aumento de la cuota de mercado de los proveedores de servicios en la nube y la creciente demanda de herramientas de automatización del diseño electrónico (EDA), sistemas que utilizan el diseño asistido por computadora para desarrollar placas de circuitos y microprocesadores.
La frontera entre las tecnologías de información (TI), tradicionalmente enfocadas en datos, y la tecnología operativa (OT), que abarca el hardware y el software, es cada vez más difusa. Por ejemplo, algunas empresas ya utilizan python, un lenguaje de programación de TI, para programar PLCs.
El siguiente paso será el desarrollo de PLCs virtuales. En lugar de dispositivos independientes con hardware específico para gestionar la automatización industrial, esta nueva generación de controladores funciona con hardware informático estándar y emula los PLC de forma virtual, posiblemente desde ubicaciones alejadas de la fábrica física. Estos podrían suponer una gran disrupción para el sector manufacturero y están siendo adoptados por grandes empresas como Siemens.
La nueva generación de fábricas conlleva sus propios retos. La ciberseguridad es primordial. Un centro de datos centralizado presenta un importante punto potencial de falla que las empresas no pueden permitirse. Pero también es más difícil de vulnerar y más fácil de actualizar, incluso con los últimos parches de seguridad.
Desde la ciberseguridad hasta los semiconductores, desde el software hasta los robots físicos, las fábricas inteligentes del futuro representan una oportunidad de crecimiento considerable para muchas empresas y, por tanto, una atractiva oportunidad de inversión temática.
*Este artículo fue originalmente publicado por Pictet en Thematic investment opportunities in smart manufacturing | Pictet Asset Management